You need:
- A motor/gearbox.
- An Arduino Pro Mini (I guess you could use any 328Mega Arduino, but the Pro Mini is small and cheap).
- A programmer for the Arduino. A USBASP or Serial adapter. (A USB equipped Arduino, if you have one, can be used as either sort of programmer too, but dedicated programmers are cheap and easier to use).
- An H-bridge board that allows the Arduino to drive the motor. I used the L9110S.
- Some parts to mount the motor and connect it to the torque rod that drives the tail surfaces. I designed and 3D printed mine, but they're not complex so you could equally make them out of balsa and plywood.
- A small tension spring that pulls the gearbox output back towards the centre of its swing. I robbed a joystick centring spring from an old broken transmitter. I guess you could use a rubber band instead, but a metal spring is more durable and reliable.
- Thin gauge piano wire for the torque rod drive, the 'birdcage' links on the rudder (and elevator if required), and the small pins that secure the spring ends. The last short ones you could actually use bits of dressmaking pins, but for the torque rod and birdcage you need some longer pieces.
- Bits of thin electrical wire to connect it all up, and some competence at soldering.
- A capacitor (about 0.1 microfarad) to solder across the motor terminals. I'm not sure if this is necessary, but it's generally recommended for brushed motors and reduces electrical noise and motor brush wear.
Items 1 to 4 can be bought on Ebay, and each item can be had for about £2 or less.
The motor/gearbox I'm using is the 12V 600 RPM one. Search for 'N20 12V Motor Gear box' The 300 RPM one should also be okay.
https://www.ebay.co.uk/itm/6-12V-300-60 ... 2390504738
Arduino Pro Mini
https://www.ebay.co.uk/itm/1-2-5-10PCS- ... 2178637340 Ignore the 'nano' in that description - Arduino Nanos are a bit bigger than pro minis (!) and have a USB interface built-in.
USBASP programming tool
https://www.ebay.co.uk/itm/New-USBASP-U ... 1938838504
H bridge
https://www.ebay.co.uk/itm/For-Arduino- ... 1437337515
The 3D printed parts are:
A plate to mount the motor/gearbox with an attachment point for the centring spring.
You need some tiny screws (smaller than M2) to fit the threaded holes in the gearbox. One source of these (the one I used) is to buy a second motor / gearbox and rob the screws that attach the gearbox to the electric motor and cut them down to length.
A coupler that joins the gearbox output shaft to the torque wire and holds the 'crankpin' that the other end of the spring rides on.
I used a mount for the plate as one of the fuselage formers in the Pulstar. The motor / gearbox on its mount plate on my Pulstar is slid into this mount upwards through an open hatchway on the bottom of the model behind the cabin area. With hindsight, It might have been better to fit it under the wing opening as there is plenty of room there to also fit the Arduino, H-bridge, receiver and ESC for the main (propeller) power motor. - that would help move the c.g. forwards. The mount is 17.4 mm wide (11/16 inch) and this sets the internal width of the model fuselage, if you use it as a fuselage former.
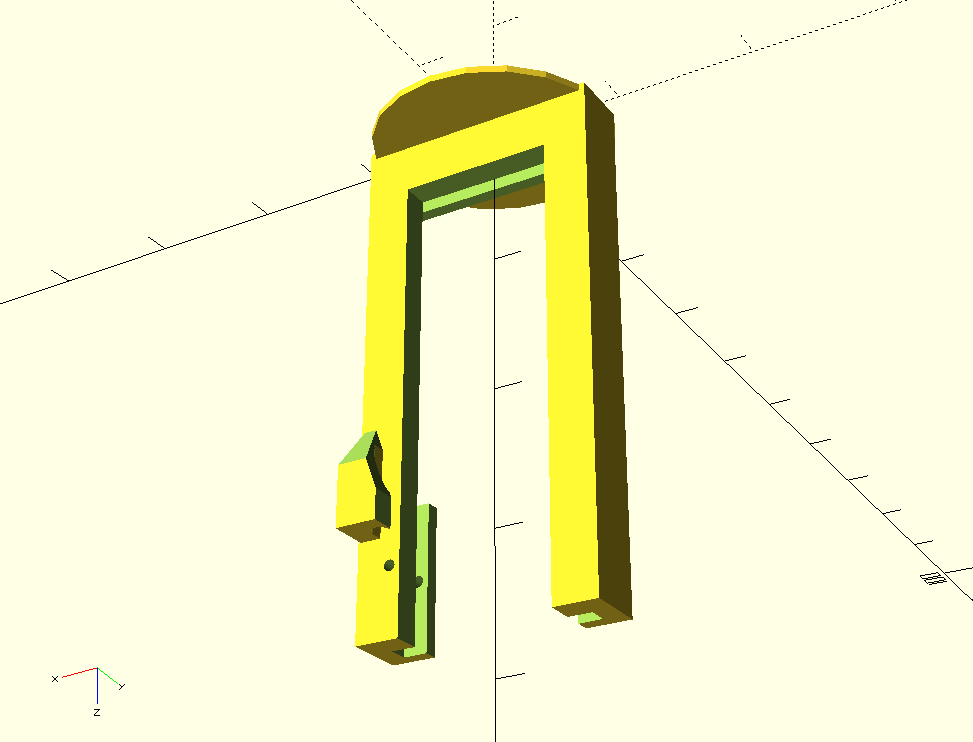
- mount.png (10.51 KiB) Viewed 5682 times
The circular plate shown at the top of that image is just a 'skirt' or 'raft' that helps the print stick to the print bed when printing (it prints upside-down compared to how it's shown there, but the image shows it the right way up for the Pulstar as you want the torque wire output up near the top of the model). You can cut away the circular part after printing.
The 3D print files in STL and OpenSCAD format are attached.
You power your receiver via the motor ESC in the usual way, and connect the main power battery negative (which is also the receiver negative via the ESC) to the Arduino GND. If you're only using a 2-cell main power battery, then you can power the Arduino by connecting the main battery positive to 'raw' or 'V-in' (NOT VCC or you will destroy the board). If you need a 3-cell main power battery then the fully charged voltage is on the limit of what an Arduino can accept on it's V-In or 'raw' terminal. You may get away with it, but it would be safer to run the Arduino by connecting the receiver positive, powered by the motor ESC at 5V, to the Arduino's VCC pin.
You then only need three wires connecting the three receiver outputs to 3 pins on the Arduino - the Arduino and receiver will already be sharing the same GND via their power supplies. 'Rudder' on pin D7, elevator on pin D6, and 'auxiliary' on pin D5.
The auxiliary channel controls the fraction of time that the pulsing motor is powered. It's best to work it (using a modern transmitter) with a two-position switch. You can set one switch position to give -100% output which stops the motor altogether - useful before launch or after landing - and the other switch position only needs be set to about -75% so that the motor is only powered about 20% of the time - this still gives plenty of drive power while minimizing the drain on the battery (about 200 mA - one fifth of an amp).
Rudder and elevator end points and elevator sub trim can be adjusted to give the desired amount of throw and speed. My Arduino sketch puts the on-board LED on when pulsing right and off otherwise. You can use this indicator to get an idea of the pulse rate and set the aux channel before you even connect the motor. When the sketch starts but it's not receiving any pulses from the receiver, the motor is disabled and the LED flashes in groups of three.
I connected the two channels of the H bridge board in parallel to drive the motor. Not really necessary as one channel can handle the motor current, but there are two channels so why not use both. Connect the battery power positive to VCC on the H bridge board (NOT to VCC on the Arduino as already described above). Connect battery power negative to GND. Connect Arduino D2 to IA1 and IA2, Arduino D3 to IB1 and IB2. Connect one terminal of the pulser motor to OA1 and OA2 and the other terminal to OB1 and OB2. As mentioned above it's recommended to solder a 0.1 uF capacitor directly across the motor terminals.
I removed the 'terminal block' from the H bridge board to save size and weight but beware that the pins are a very tight fit through the PCB holes and even with careful de-soldering I ended up pulling the tracks off the PCB

If I ever make another one I shall cut / grind away the connector block rather than try to unsolder it.
Arduino sketch is attached.